El acero ligero de la Ford Bronco podría hacer que la marca reconsidere fabricar camionetas de aluminio
El Ford Bronco incorpora un nuevo acero más ligero que le permite quitar peso de su carrocería

Ford Bronco 2021. / Foto: Cortesía Ford. Crédito: Ford | Cortesía
El nuevo Ford Bronco 2021 está de moda, y a partir de menos de $ 30,000 dólares, es barato para lo que obtienes. Una de las razones de ese bajo precio es su construcción, que utiliza mucho acero en la carrocería y el marco en lugar de materiales más livianos y costosos. Pero más barato no es lo mismo que más simple.
Los huesos aparentemente básicos del Bronco se encuentran en realidad entre las partes más interesantes del nuevo SUV de Ford: es el primer vehículo de pasajeros en usar un nuevo tipo de aleación de acero de ArcelorMittal que algún día podría suplantar al aluminio como el metal liviano preferido por los fabricantes de automóviles.
La clave de estas aleaciones de acero de la llamada “Generación 3” es que el metal se puede estirar en formas más delgadas y ligeras sin perder resistencia. Los fabricantes de automóviles han estado buscando materiales más livianos y resistentes durante décadas, recurriendo a todo, desde aluminio hasta plástico y fibra de carbono en una búsqueda por ahorrar peso. Pero, evidentemente, todavía hay formas de hacer un mejor acero.
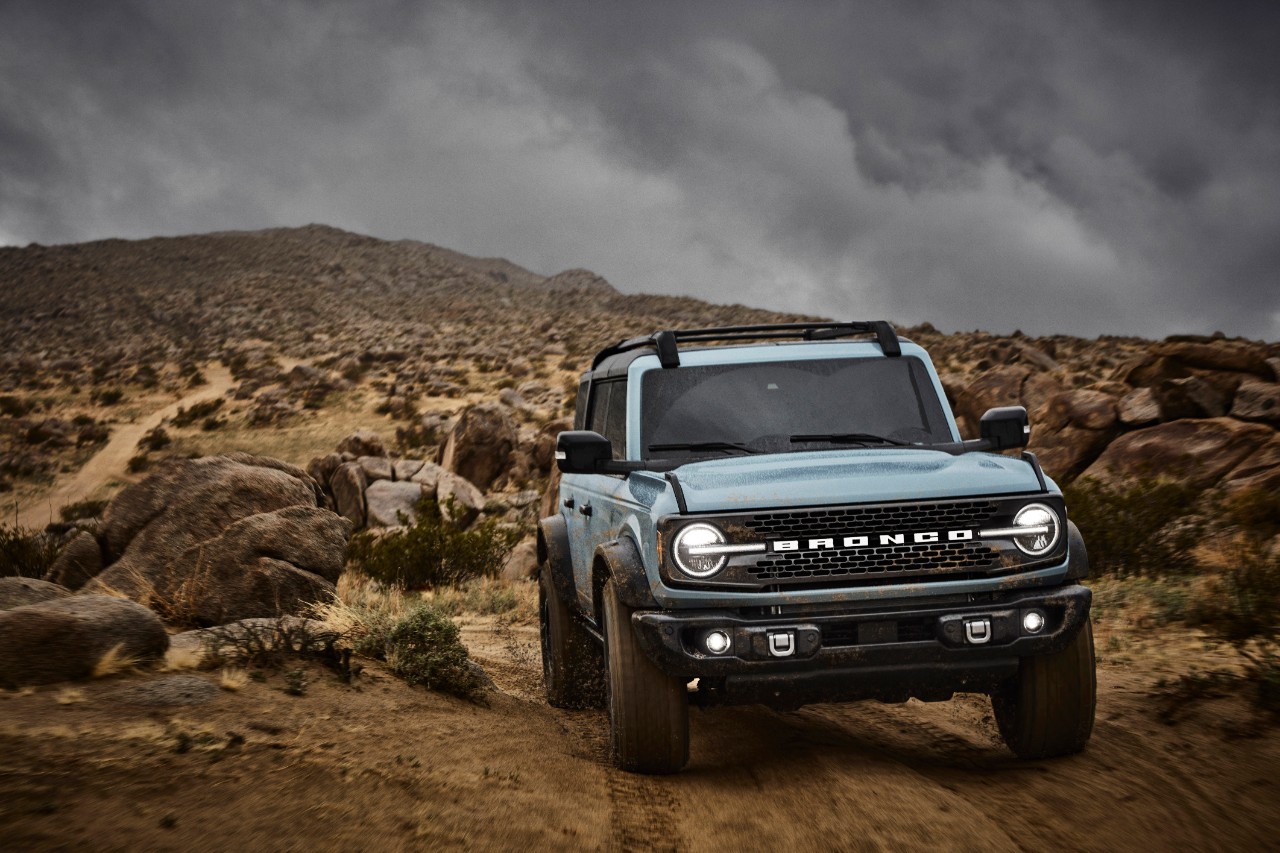
Al trabajar en estrecha colaboración con Ford, el proveedor global ArcelorMittal pudo diseñar un material que podría fabricarse hasta un 35% más delgado que antes, manteniendo la misma rigidez. Sólo hay un problema, si bien la ciencia detrás del nuevo acero en el Bronco no es un misterio, aún es difícil hacerlo a gran escala. ArcelorMittal necesita descubrir cómo hacerlo antes de que hablar de llevar la lucha al aluminio se convierta en una realidad.
Michael Lizak, el Coordinador Global de Tecnología Automotriz de la compañía, dijo a The Drive que el primer obstáculo es la estrecha cooperación entre ArcelorMittal y un fabricante de automóviles como Ford que se requiere para producir de manera segura y correcta acero de Generación 3 para su uso en un automóvil producido en serie. El material no solo se envía a Ford en un rollo masivo para ser prensado en piezas terminadas. De hecho, gran parte del endurecimiento del acero tiene lugar en las instalaciones de Ford. El acero gana fuerza una vez que se presiona para darle forma, y su dureza final solo se obtiene después de mantenerlo en un horno durante veinte minutos a casi 350 grados Fahrenheit durante el proceso de horneado de la pintura.
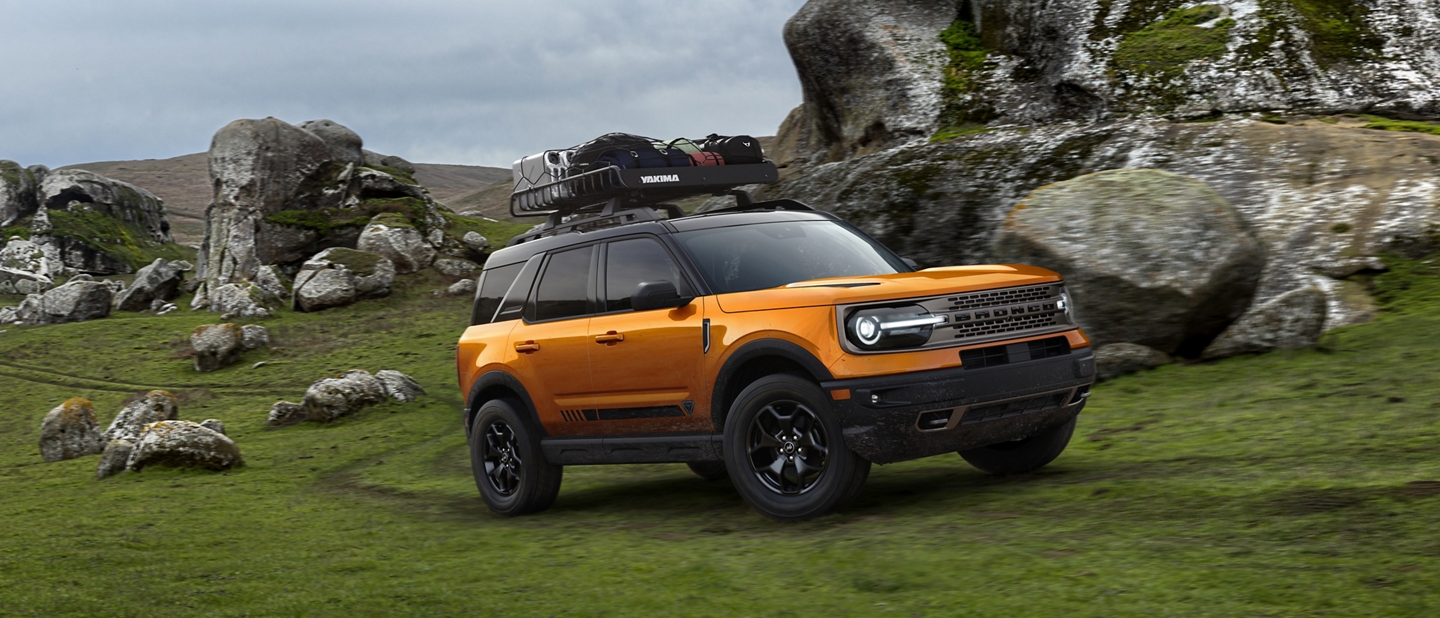
Es por eso que este acero no es tan fácil de trabajar como otros. Los empleados de Arcelormittal no solo deben ir a la fábrica de Ford para asesorar a sus ingenieros sobre el mecanizado y el endurecimiento del metal, sino que el proceso para cocinar el acero justo antes de que llegue a ese punto es intensivo. El acero en factores de forma difíciles de manejar debe calentarse a temperaturas extremadamente altas pero precisas, enfriarse a temperaturas igualmente precisas, un proceso conocido como enfriamiento, y luego recalentarse nuevamente por una cantidad de tiempo muy específica y nuevamente a una temperatura específica. Si algo de este meticuloso calentamiento y enfriamiento se realiza de manera desigual, el metal terminado simplemente no tendrá las propiedades requeridas.
Sin embargo, a pesar de lo avanzados que están estos materiales, estos nuevos aceros solo se utilizan en pequeñas cantidades en el Bronco, alrededor del 5% del acero total utilizado. Puede que esto no parezca mucho, pero Lizak estima que representa algo así como 150 libras de ahorro de peso.
**********
TE PUEDE INTERESAR:
– Tesla abre la nueva estación super charger más grande del mundo en Shanghai
– Cierra 2020: Estas fueron las tendencias de compra en autos este año